The AV supply chain has been struck by an unprecedented series of incidents in the last 18 months, and things are set to get worse before they get better says Paul Milligan.
If you’ve tried to buy any AV-related product in the last 18 months the chances are it won’t have been delivered on time, and was delayed anywhere from two weeks to six months to even a year. The one constant in all interviews I have conducted since the Covid-19 pandemic hit in early 2020 is that products have become much harder to get hold of than at any time in the last 10-15 years. And the pain is being felt by everyone, regardless of geographic location or the type of business you are running. It’s not called a supply chain for nothing, component suppliers are struggling to meet demand (we’ll explore the reasons for that later on), so manufacturers can’t build the products in time, which means integrators are facing delays in projects, and end users aren’t getting to use the tools they need to move their organisations forward.
And it’s not just one product suffering these delays. As the AV world becomes ever more indistinguishable from the IT world, every part of the AV ecosystem has been affected, from speakers to switchers, from flat panels to PTZ cameras, no one is immune. Despite it being nearly six decades old, our reliance on the humble microchip has become absolute in recent times, if they become in short supply, as they have done, then we all struggle.
What we have seen in the last 18 months is a perfect storm.
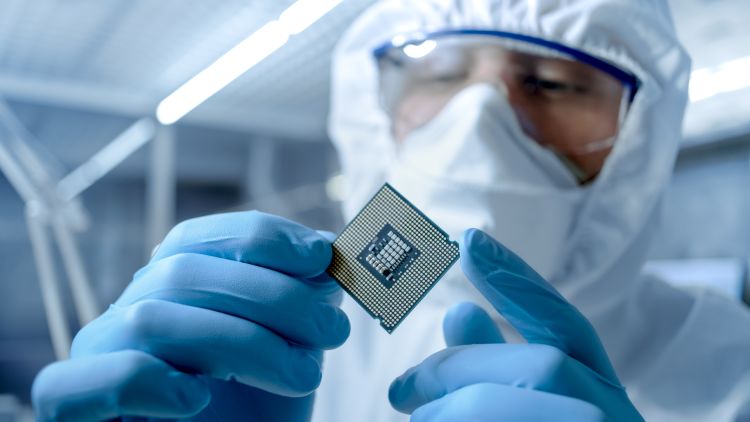
A global pandemic shut down factories in the manufacturing hotspots of China, Japan and Taiwan in early 2020. The spread of the pandemic drove demand for products in the AV supply chain rise in staggering amounts overnight. The spike in demand was met perfectly by a fall in supply. Alongside the Covid pandemic, there were a host of other, quite incredible factors that affected the global supply chain. President Donald Trump had started a trade war between the US and China during his time in office, causing many Chinese companies to stockpile products once trade sanctions had been put in place. A series
of high-profile fires in factories and freak weather in the form of droughts and extreme cold caused factories around the world to stop production when it was needed most.
The pain didn’t stop there.
The instigation of the Brexit agreement in January and the Suez Canal blockage in March caused more devastation to a supply chain still reeling from events in 2020. No one was immune. Apple announced revenue would be $3-4bn lower in Q2 2021 due
to ‘supply constraints’, and Samsung, the world’s second-largest buyer of microchips after Apple, had to postpone the launch of its high-end smartphone due to the shortage, despite also being the world’s second-largest producer of microchips. Even if you made them you couldn’t meet the demand.
The chip shortage was heightened by the pandemic. When it first struck many companies cut their orders for chips thinking demand would fall, which led suppliers to reduce capacity but demand for consumer electronics rose during the pandemic, which lead to shortages. These shortages have also been exacerbated by companies over ordering components to build up inventory, afraid of being caught short again. Samsung is believed to be struggling to fulfil orders for the chips it makes for its
own and others' products, and Qualcomm, another leading chip manufacturer is thought to have the same problem.
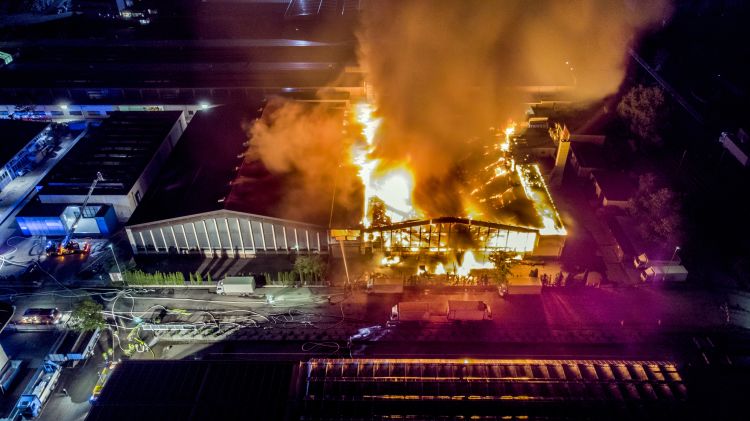
The chip shortage, dubbed ‘chipageddon’ in some quarters which gives you an idea of how seriously some people are taking it, is also driving fears it could slow economic recovery after Covid-19 has gone away. So plans are afoot to boost production, however it’s not a quick or easy fix; “It takes about 18 to 24 months for a plant to open after they break ground," Edison Investment Research analyst Richard Windsor told the BBC. "And even once you've built one, you have to tune it and get the yield up, which also takes a bit of time. This isn't something you can simply switch on and switch off.”
The rollout of 5G infrastructure is also adding to chip demand. TSMC and Samsung, the two leading chip producers have invested billions getting the 5-nanometre chip-manufacturing process established, but that is not the widespread approach and the sector has suffered from under-investment, and we are seeing the results of that now.
The trade war between the US and China is undoubtedly affecting the global supply chain too. In his short time in office new president Joe Biden has appealed for US businesses to make the country a world leader in computer chips and has asked for $50bn in funding to support domestic chip manufacturing. One company already responding to his call is US manufacturer Intel, who is to spend $20bn (about €16bn) on two new plants in Arizona. However, the US still has a long way to go to address the global imbalance. The US-based Semiconductor Industry Association has reported that 75% of global manufacturing capacity is in East Asia.
Economist Rory Green from TM Lombard investment group estimates two Asian nations account for 83% of global production of processor chips and 70% of memory chips. "Like Opec was for oil, Taiwan and South Korea are near monopoly producers of chips." That might not change as quickly as the EU or the US would like, TSMC, who call themselves ‘the world's most advanced chip-maker’ and is the world's biggest contract manufacturer, has announced it is spending $100bn to expand capacity over the next three years, including a huge plant in Arizona.
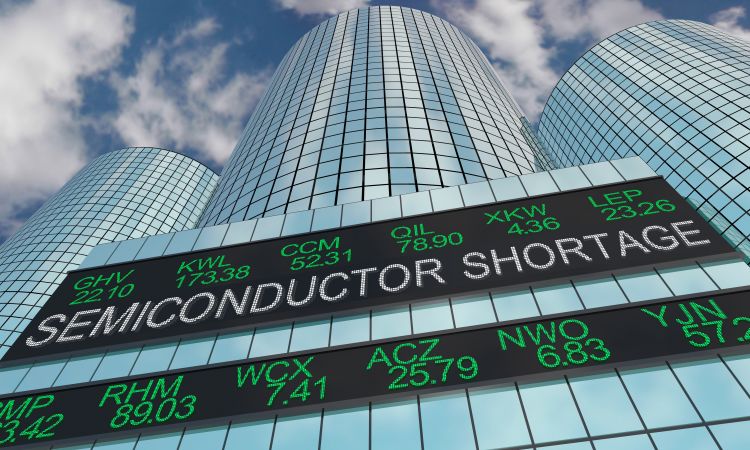
Because of the increasing proliferation of what were once seen as strictly IT products and components in modern pro-AV products, it’s hard to separate IT supply chain issues with AV supply chain issues. But it’s clear the AV industry has and will continue to suffer too; “The impact will be felt across the large area LCD displays containing TV, IT and pro-AV displays,” said Sanju Khatri, consulting director of displays, pro AV and consumer devices at research firm Omdia, speaking to Commercial Integrator magazine. She added that although this impacts consumer TVs and other industries that rely on displays, the impact on pro-AV could be more pronounced since pro-AV is generally not a high priority to chip manufacturers.
“We think the impact on pro-AV displays will be more pronounced simply because the buying power of the pro-AV displays is less compared to the big TV brands,” Khatri says. “This may lead to either increased price of the pro-AV displays or reduced profit margin of pro-AV display manufacturers.” Some high-margin products like videowall panels, high brightness displays and panels larger than 90-in should be further up on the list, Khatri adds. The supply chain issues don’t stop there however, in addition to semiconductors, there is also a limited supply of glass for LED displays, further impacting our industry.
A chain of big factory fires in the last 12 months also caused huge problems to the supply chain. A fire in March this year took out the first floor of the Renesas Electronics factory, just north of Tokyo. Renesas Electronics is the second largest semiconductor manufacturer in the world, and it is believed it will take three to four months before it is up to full capacity again. Another fire in October at the Nobuoka semiconductor plant in Nobeoka, Japan stopped production of large-scale integrated circuits used in audio equipment and other products. In July 2020, a fire at a Nittobo plant in Fukushima, Japan disrupted supplies of fiberglass to ABF substrate producers, which in turn caused delays at manufacturers of high-end servers, networking chips, and CPUs. As we said above, its not called a supply chain for no reason and if any part of the process is delayed, it has a clear knock-on effect even if that isn’t immediately obvious.
As if a global pandemic and a trade war between the two most powerful countries in the world wasn’t enough to suffer in the same period, freak weather has also greatly affected the global supply chain. Plans to ramp up production of chips in Taiwan were severely hampered by droughts, which then affected the water supply to its factories. Manufacturer TSMC said needs 156,000 tonnes of water per day to operate and it has even begun to transport water in via lorries to make up the shortfall.
The problem wasn’t just confined to APAC, February's freezing weather in Texas closed chip-making plants there too. Temperatures in Texas reached -18C, the lowest recorded in the state in more than 30 years, and Samsung and NXP were among the companies who had to halt production. In what has rapidly become a ‘it never rains but it pours’ 12 months for those working to keep the supply chain going, the blocking of the Suez Canal, which carries 12% of global trade through it every day, was another hugely unfortunate and unwelcome event. The grounding of the Ever Given container ship for six days in March held up an estimated $9.6bn of trade along the waterway each day (according to data from Lloyd's List). Some vessels chose to reroute to avoid the Suez Canal, but that added another eight days journey time, again causing more delays to a global supply chain that could ill afford it.
So what is the outlook? According to figures in the industry it’s not great, in the short term anyway. Cisco chief Chuck Robbins told the BBC: "We think we've got another six months to get through the short term. The providers are building out more capacity, and that'll get better and better over the next 12-18 months." According to Bank of America research it expects semiconductor industry supply constraints on both wafer and substrates to only partially ease in the second-half of 2021, with new technology (such as 5G chips) to have problems extending into 2022. According to research group Gartner the worldwide semiconductor shortage will last throughout 2021 but will recover to normal levels by Q2 2022. Intel CEO Pat Gelsinger told the Washington Post it may take a little longer, “I think it’s a couple of years until you are totally able to address it. It takes a couple of years to build capacity.”
In a traditional consumer market when demand outweighs supply the cost typically rises, those who have supply can profit. Will we see that here? Possibly in the very short term, as companies try and claw back some lost revenue from 2020 and 2021, but it has to be balanced with the fact that components such as computer chips generally fall in price every year, so it may balance itself out. I think one thing we can say is that given the pain suffered by everyone in the supply chain in the last 18 months, products certainly won’t be getting any cheaper, and we all may have to become more patient.