The new National Museum of Qatar tracks the country’s growth over the decades fusing incredible architecture with AV to create an immersive experience. Paul Milligan reports.
In an ever evolving skyline, the new National Museum of Qatar has certainly made a dramatic addition. Designed by award-winning French architect Jean Nouvel, the museum’s modern exterior is adorned with 539 curved disks, intersections, and cantilevered angles, all inspired by the local desert rose, a natural phenomenon found in Qatar where sand particles form into petals.
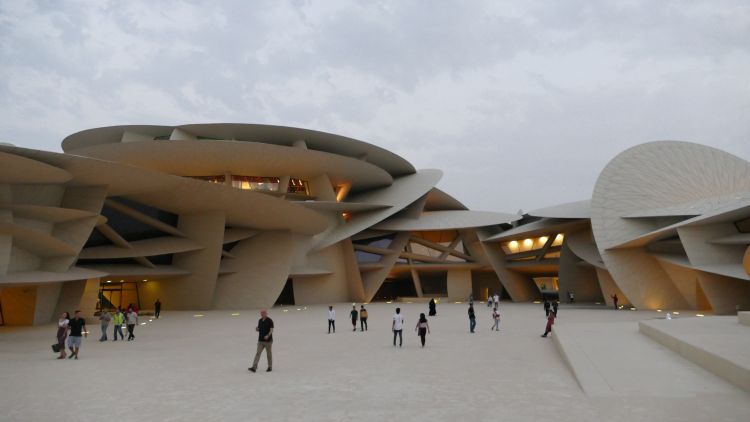
The desert rose also inspires the interior, which consists of large, irregularly shaped walls, ceilings and floor panels. The museum features a 220-seat auditorium, dedicated library for study and research, rooftop restaurant, and newly landscaped park. It is home to more than 86,000 square feet of exhibit space, with multiple interconnected galleries.
Designed to be both immersive and experiential, the exhibits are spread over eleven galleries and across 1.5km of walkways. Thematically, the museum is split into three chapters; ‘Beginnings’, ‘Life in Qatar’ and ‘The Modern History of Qatar’. Galleries 1 to 6 cover the history of the country, galleries 7 to 9 cover its more modern history, with gallery 10 covering the recent discovery of oil and gas. The theme of Gallery 11 is ‘Qatar Today’, and offers a look into the future by the ruler of Qatar, HH Sheikh Tamim bin Hamad Al Thani, including a look at the soccer World Cup which the country hosts in late 2022.
Tasked with installing the audio in halls 1 to 9, and designing and installing the AV for galleries 10 and 11 for the client QMA (Qatar Museum Authority - the government department that runs all museums) was local integrator Techno Q.
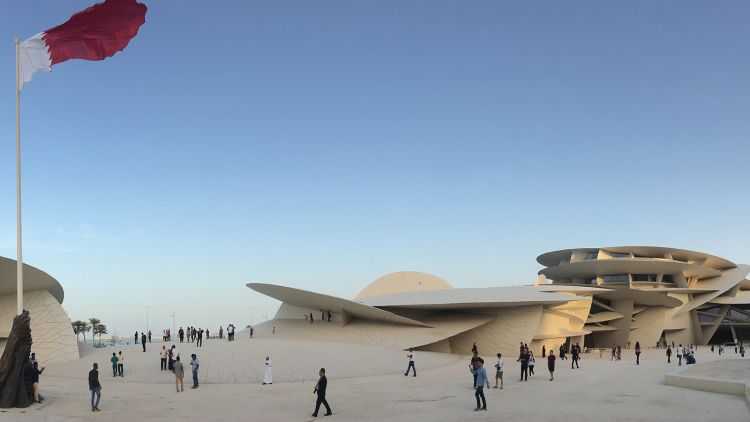
The brief to Techno Q was to provide a multisensory experience using multi-channel audio, lighting, and LED displays to work in tandem with the curved architecture and mirrored walls, ceilings, and floors to create total immersion. “When you stand at one corner you can see in front of you or a corner behind you, the reflections create the immersion,” explains Ahmed Marei, who was the commissioning manager from Techno Q. The project was set into different phases, with initial construction in the first phase, and gallery 11 in the second batch.
Galleries 1 to 9 feature Panasonic 10,000 lumens PT-RQ13KE projectors alongside Meyer Sound audio in amongst the museum artifacts. The installations in 1 to 9 were completed in a joint venture between Qatar-based design and build group Man Enterprise and museography specialist Empty S.L. from Spain. The museum’s immersive audio design was created by Switzerland-based multimedia agency Idee und Klang. Gallery 10 features 35 Plura flat panel displays, in sizes ranging from ten 21.5-in screens to seven 86-in screens.
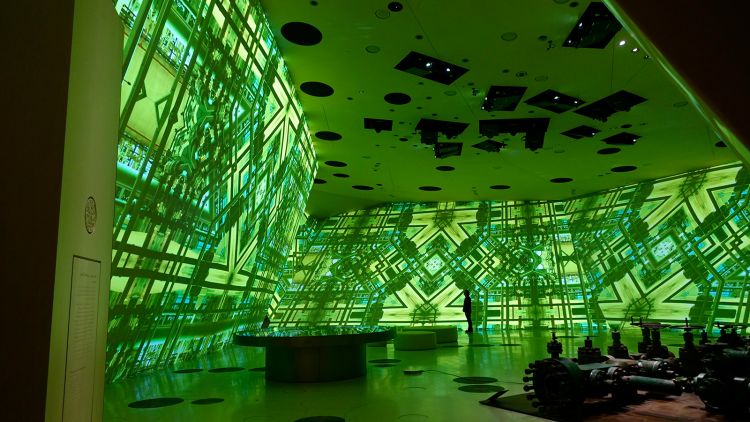
Techno Q was awarded the work in gallery 11 due to its previous work on the project. Gallery 11 sees a total of 14 walls covered with mirror-finish glass panels, with video integrated with synchronous audio and lighting on each wall. At the planning stage Techno Q was given a rendering of how the client wanted gallery 11 to look from a media perspective i.e. the screen placement and how they wanted the finish of the gallery to look. “They didn’t want the audience to be looking at screens, instead they wanted them to be looking at glass finishes across gallery 11,” explains Marei. “From that render of the design all the engineering and technical sides of the project were completed solely by us, it was designed and built by us, we chose which screens to go for. We then had to look at how we were going to plan the maintenance of the screens, how we would plan the structures of the screens, what should the pixel pitch of the screens be? Could the audience see any broken pixels in their view? Where could the speakers be placed? All this detail, from an AV perspective, a maintenance perspective, a structural perspective was designed by us.”
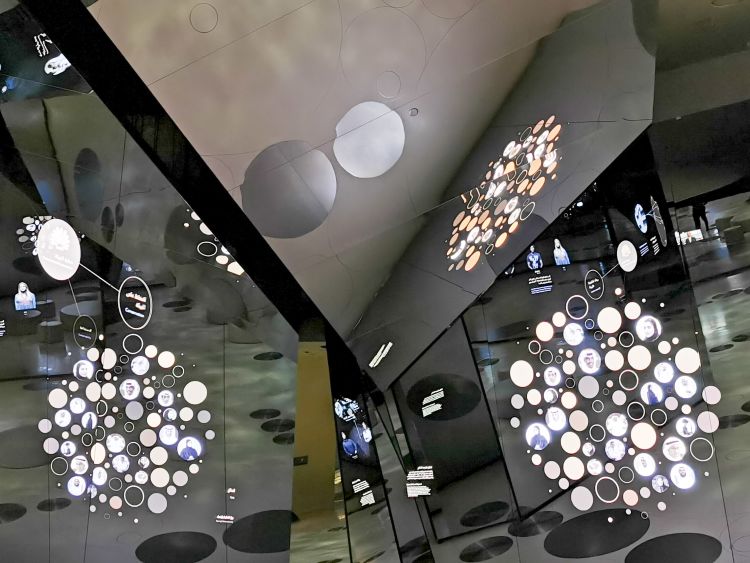
One of the challenges for Techno Q was to achieve seamless AV equipment integration alongside the curved and interlocking discs meshed in cantilevered angles along the walls and ceilings. The projection options considered by the architect (4K rear projection and LCD panels) were assessed by Techno Q but were both unsuitable because rear projection required operable space behind, which there wasn’t due to the quirks of the architecture, and LCD displays did not allow the desired brightness, seamlessness, and scalability. Marei takes up the story; “For rear projection, even a UST model didn’t seem to work since it had the risk of projecting hot spots and would render the images unpleasant. For LCDs, apart from limitations of resolution and fixed size, bezel structure would undo the image seamlessness.”
Given the nature of the setting and client requirement, Techno Q decided to install modular LED tiles, with 1.9mm pixel pitch since it allowed, due to its smaller cabinet size offering, the customisation required to match the irregular surface dimensions, as well as meet the resolution specifications. The combination of depth and brightness (1,500 nits of LEDs versus 500 nits from LCDs) was enough to convince the client to choose LED, so once the decision was made Techno Q worked with manufacturer Daktronics for a customised LED configuration. Techno Q also brought on the expertise of staging company Gerriets to supply the highly accurate sliding mechanism.
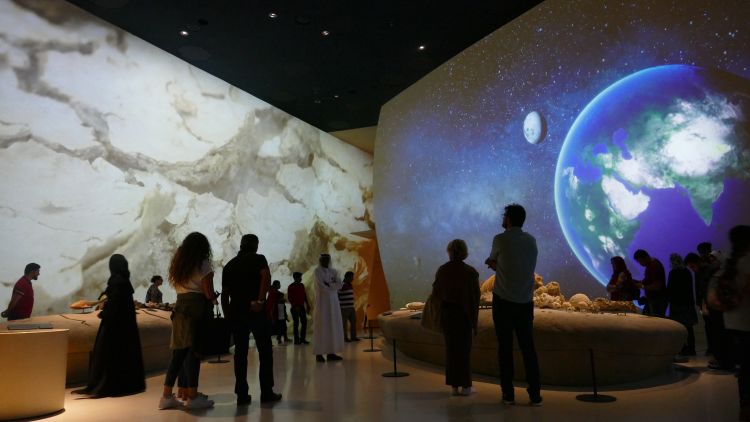
Even though it was easier to install than other display options, the LED did pose a challenge in its serviceability, because all LEDs require front tolerance for accessibility and the front is covered with large mirror-glass panels. Techno Q looked for a feasible solution and came up with a giant structure to house all of the LED sitting on a sliding rail mechanism. There was little room for error for the integrator when installing this system explains Marei; “The whole LED screens, along with its secondary support structure are on tracks so we can maintain them. They're installed with a gap of 5mm from the mirror so that when we need to perform maintenance, we can pull the screen back, there is also a mechanised ladder to access the top or bottom areas.” The engineer accesses the screen from the front, performs the required maintenance and then comes out. “This part was one of the most critical to get right, we had to make sure the ergonomics were properly designed for engineers to be able to move around the structures and to be in front of the screen and reach the speakers.”
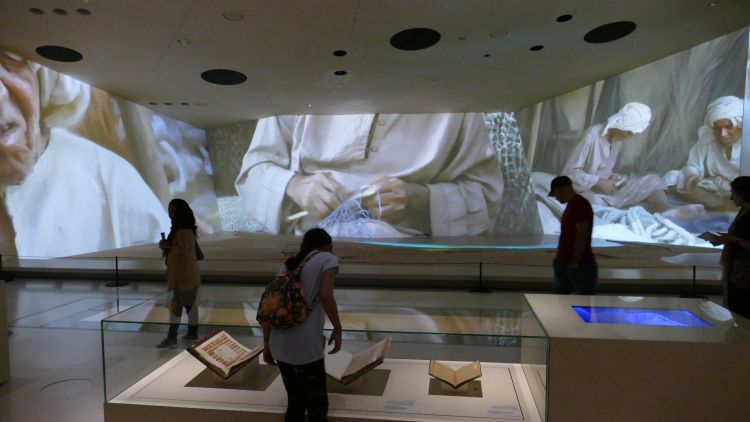
Each of the 14 walls contain anywhere from a 3x6 wall of LED tiles, up to four uses of an 8x6 configuration, one 7x8 and three 8x8 configurations. Gallery 11 includes just short of 600 LED tiles in total. To add to the difficulty of this section of the install, the combined screen structure weighs one tonne each, and each screen must move forward to the operational position but has to stop at 5mm exactly and must move back to the maintenance position and lock itself. To plan all these details involved multiple parties says Marei, “The glass contractor, the civil contractor, the structural contractor were all involved to make sure that the result meets the requirement.” Another factor to be taken into consideration was that the screens were not straight and were tilted at 20-degrees. “We have to make sure the screen stops at the right angle. Everything had to be completed as it was in the drawings. It wasn’t a case of installing the screens and then building the glass structure around it, we had to follow the angles and points of installation exactly, and include exactly the right amount of gap,” adds Marei.
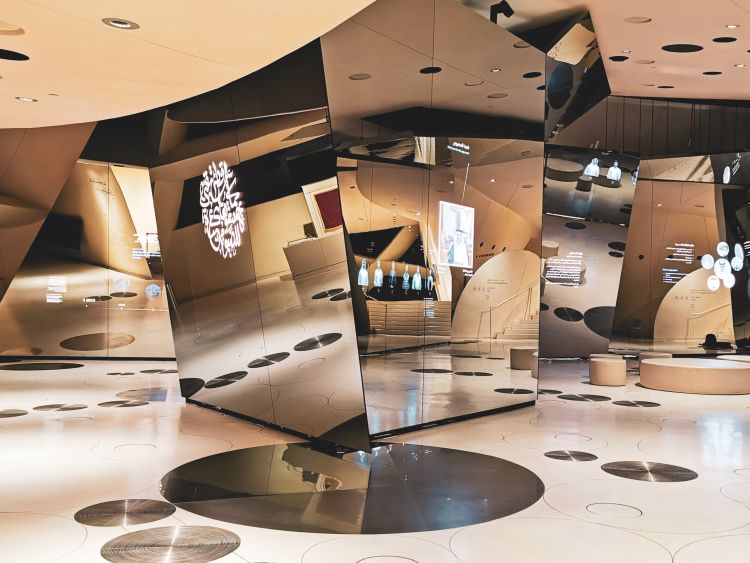
With only 5mm of space to play with between LED and mirror glass, was heat not an issue? “To Spectest the install we installed temperature sensors around the screens. We created a test environment using three cabinets and completely blocked the surroundings to see what would happen in the worst case scenario for the system and how it would respond. The temperature level did not go beyond what is acceptable,” says Marei. In additional stress tests, Techno Q also put a completely white light on the screen, with a glass in front of it and tightened the surrounding to see how it responded and “it did not cross any of the threshold values,” adds Marei.
Four Dataton Watchpax 60 media servers of 8 outputs work with 2SI and SQD pixel mapping technologies to map the content while it is routed to the screens via a Grass Valley 64x64 video router. A Dataton Master media server generates and distributes time codes for audio and lighting outputs to ensure a seamless flow of content. Content runs on a loop explains Marei, “There is a loop of around 48 minutes, all the content is divisible of 48, either 12 or 24 minutes, to make sure we have one cycle of 48 minutes and all the other content sits in that specific cycle.” Rosco’s themed lighting was chosen to accentuate the lighting ambience and is augmented by Crestron CP3 control processor and Medialon show controllers via a DMX protocol.
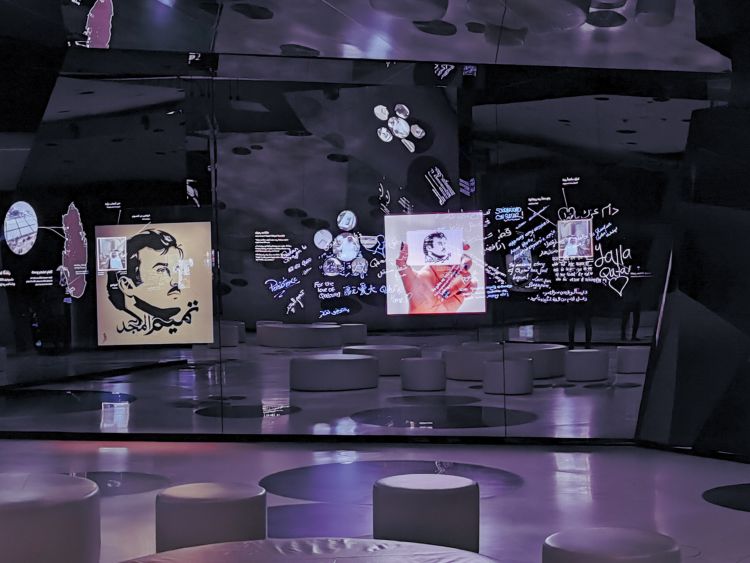
Each gallery has its own theme, and with that comes different accompanying audio. Like the display technology, the audio also had to fit around the unique architecture of the museum. “We specified 64 channels for each gallery – almost 700 speakers in all,” says audio scenographer and designer Daniel Teige. Meyer Sound provided the loudspeakers for the project, which was mixed using Spat Revolution. Placement of the loudspeakers was also an issue says Idee und Klang company founder Ramon De Marco. “The architects were adamant that they did not want to see any speakers. They originally wanted speakers only on the ceiling, which, depending on the gallery, ranged from 4m to 20m high. Achieving any kind of directionality would have been pretty much impossible, and eventually we were able to lobby for locating some speakers at the bottom of the walls, where we had about 8cm of clearance. Meyer Sound had a compact speaker, the UP4slim, that we were able to implement in that limited space.”
Most of the speakers are situated below a small skirting board under the glass, with a mesh in front of the skirting. The other speakers are located in the ceiling, which send out audio with voice content within. Any room with mirrored walls and ceilings provides a tough environment for sound, so Techno Q commissioned a full acoustic study of gallery 11 by acoustic consultant Ivana Rossell, which considered every reflection angle, both horizontality and vertically, for each speaker. A full sound calibration using smart audio analysis and analysis software made sure it simulated the average height of the audience standing in the galleries, to make sure that the audio would reach that particular point.
“All the audio was calibrated so it’s as uniform as possible, so that we don’t have too many frequencies that are cancelled out due to the reflections,” says Marei.
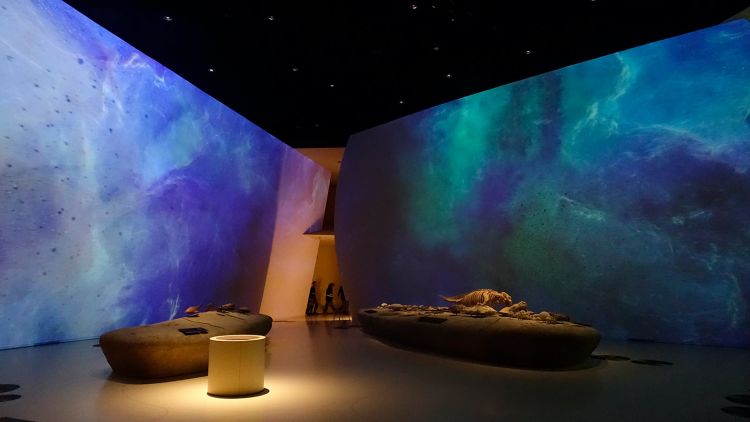
Unlike most AV projects there were no access issues for Techno Q says Marei, as the project was well planned from the outset. “The client and the main contractor understood there had to be a provision for the technical systems and it was clear from the drawings prepared beforehand that it was completed by a company who was in sync and understood the design requirement. It was not a project where you have to tell people ‘you forgot to have a cable there’ etc. You cannot always omit surprises during a project, but there were far less on this installation as it was very well planned.”
Moving forward Techno Q has staff on-site and is also monitoring the AV remotely to make sure everything runs as it should as part of its service contract.