The deployment of AR glasses for its technicians by a car manufacturer in Turkey is producing a series of benefits.
Augmented Reality (AR) technology is far from new. But so far it has suffered from a similar gimmicky perception as 3D glasses did and barring a few small or one-off retail projects is not being employed in substantial numbers in pro-AV environments. New technology sometimes needs a shove in the right direction to drive adoption, and one project in Turkey might just be a catalyst for other companies to take a serious look at the technology. Anadolu Isuzu, a joint venture with Anadolu Group, Isuzu Motors and Itochu, is a supplier of pickup trucks, buses and minivans based in Istanbul. It has deployed VSight’s remote collaboration software on RealWear’s assisted reality devices for its technicians to increase productivity.
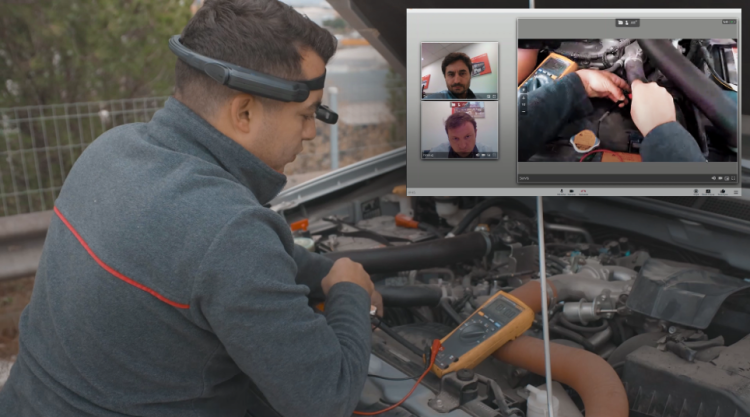
The ruggedised RealWear HMT-1 headset enables Anadolu Isuzu’s technicians to resolve mechanical issues significantly faster by connecting them with centre experts. The HMT-1 headset has been built to be hands-free so users can climb ladders or hold other machinery at the same time. It can clip onto a hard hat and runs the Android OS. It features a drop-down 854 x 480 pixel display, which is similar in size to what you would see in a 7-in tablet device.
In Anadolu Isuzu’s Academy Technology Centre there are two facilities - a technical support room and proactive online studio. Anadolu Isuzu’s technical support team is using the HMT-1 to give fast and accurate service to its customer’s vehicles within its distributor and services network. Another benefit of the technology is that it can be used in online hands-on training, enabling the wearer of the device to show part details, assembly, disassembly and adjustment procedures to attendees in the online studio. In addition, Anadolu Isuzu is using the system in remote supplier quality control processes. The devices have already driven a number of benefits for the business, including speeding up repairs – such as a door adjustment or Engine Control Unit (ECU) programming, significantly reducing travel, reducing the company’s overall carbon footprint, and improving logistics efficiencies for thousands of customers.
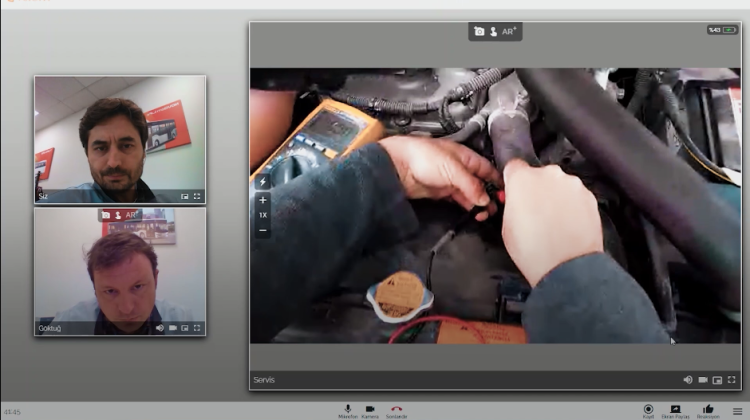
As a key part of Anadolu Isuzu’s post-sales service, the company uses vehicle technicians to service and maintain its fleet of commercial vehicles, many of which are part of the global supply chain. Prior to deploying the devices, to conduct a truck or bus repair on a stranded vehicle, Anadolu Isuzu would often send one or more technicians specialising in various disciplines to the location of the breakdown. If technicians were then unable to successfully resolve the issue additional technicians would have to travel to the location to work on the problem. Because many of Anadolu Isuzu’s customers are commercial vehicles delivering parcels on a tightly timed schedule, any delay results in dissatisfied customers and lost revenue. Given the financial and logistical implications of a stranded vehicle, Anadolu Isuzu placed a high priority on finding a better way to get a vehicle fixed right the first time.
“Our travel needs prior to the deployment were prolonging our operation and repayment time. This was a negative situation in terms of competition and customer satisfaction,” said Hakan Ozenc, after sales services director, Anadolu Isuzu. “Due to the travel restrictions that were imposed in Europe in response to the pandemic, the technology quickly became vital for us, and we revised our previous way of working. HMT-1’s running VSight software have been highly effective in our after-sales operations and importantly technicians can use both hands with the system, which is vital from an operability and safety standpoint.”
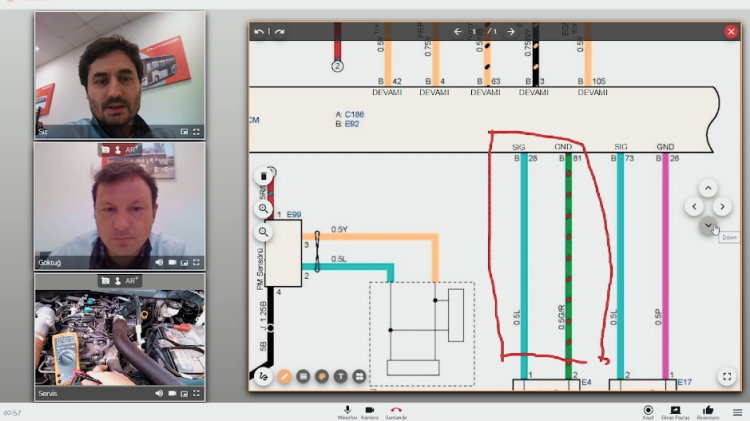
Anadolu Isuzu began its deployment of HMT-1’s in early 2020, spurred on by the pandemic and the subsequent restrictions that came into place. The numbers since that time show how important the technology has become to the company. The assisted reality devices are now being used across 25 of Anadolu Isuzu’s domestic services and nine foreign distributors across nine European countries. Since the deployment, Anadolu Isuzu has intervened in 366 malfunctions in 78 different locations over the course of a year. As there has been a significant reduction in travel, there has been a huge gain both financially and environmentally. At the same time, there is no need for warranty parts to be shipped to its warehouse. By having the ability to examine parts on site via the HMT-1 headset, Anadolu Isuzu has sped up its decision-making process and reduced its shipping costs, meaning it has gained in safety, efficiency, productivity, and cut costs and time.
“There are numerous advantages with this hardware and software, and we are able to solve mechanical problems very quickly,” added Ozenc. “Additionally, operational costs are much lower, and we are receiving a great deal of customer satisfaction. This technology has also prevented repair-related accidents, with none recorded last year since the implementation.” Going forward the use of the technology is to be expanded by Anadolu Isuzu, who is looking to ensure the assisted reality devices are widespread in all of its 92 service centres in Turkey, and amongst its 35 foreign distributors.