LED is in high demand. But do we always know what type of LED we are buying? Paul Milligan investigates.
LED has been the hottest product in the AV world for the last decade. You only have to open the pages of a trade magazine or walk around the ISE or InfoComm shows for two minutes to see a wide range of LED products from around the globe. It’s not rocket science to work out why it’s everywhere right now. Its falling in price and rising in quality, so buyers are now getting a far better product for less money than they were 5 or 10 years ago. Its super bright, quick and easy to install and requires little maintenance once built. Basically, it’s an integrator’s dream. So its not surprising then that the LED market is becoming flooded with new manufacturers looking to get a piece of this lucrative pie. The issue with such a vast array of new companies being added to the market is that users can be baffled by what’s in front of them, and also confused by the different types of specific LED technology you are getting for your money.
To help clear this up we spoke to established LED providers to go through the different LED package types, and why you would choose certain ones. The four LED package types that are widely used in videowalls are DIP (Dual In-line Package), SMD (Surface Mounted Device), GOB (Glue-on-Board) and COB (Chip-on-Board). Graham Burgess, CEO of contract manufacturers DigiLED has been involved in LED sales and installation since 1990, so is one of the most qualified to guide us through a short history lesson of LED, and its different types, starting with DIP. “When people started buying LED screens instead of cathode ray tube and FDT (Fluorescent Discharge Tubescreens), they were using a technology called DIP (also known as Through Hole technology). It’s a cylindrical LED with a dome at the end of it, and two LEDs are pushed through a PCB, hence Through Hole. It was used for outdoor screens in the early days, and you picked a combination of red, green and blue to create a pixel. The diodes that you put together to make the pixel, there were just too many of them to get a very tight pixel pitch, so its limit was 12mm or 10mm. DIP is the most robust, the most traditional of LED technologies, but used very little anymore, because there are lots of limitations with DIP.”
You will still find DIP LED screens being installed, with the majority as outdoor screens with a long viewing distance. The disadvantages of DIP are that it’s expensive to produce and has a narrow viewing angle. When viewing off-centre, the colours may appear dimmer. Burgess says DIP began to fade into the background around the turn of the century, and credits Lighthouse with the emergence of SMD, which doesn’t use three colours (red, blue and green) of LEDs, instead it makes a single point of white or black by grouping them into a single package. The resulting package can then be soldered onto a PCB. “It’s not as bright or as resilient as DIP, not as waterproof as DIP, but massively more versatile, and like all of the technologies has improved over the years,” adds Burgess.
Unlike DIP, SMD LEDs are not visibly separate, so the gap between each pixel is almost unnoticeable to the eye. ROE Visual’s range for now consists just of SMD LED, with a release of a COB-based display (more on that later) planned for later this year says Marina Prak, marketing manager, ROE Visual Europe. The big advantage of SMD is its size, it’s small so can produce tiles of just 0.4mm pixel pitch. Due to mass production, SMD is generally cheaper too. It does has some disadvantages however, its prone to damage because of its small size, and has a poorer heat transmission rate, which can result in higher maintenance costs over time. The inevitable comparison between DIP and SMD also raises another issue for buyers says Burgess, and one they may not know the importance of, about the comparative differences between gold thread and copper thread technology.
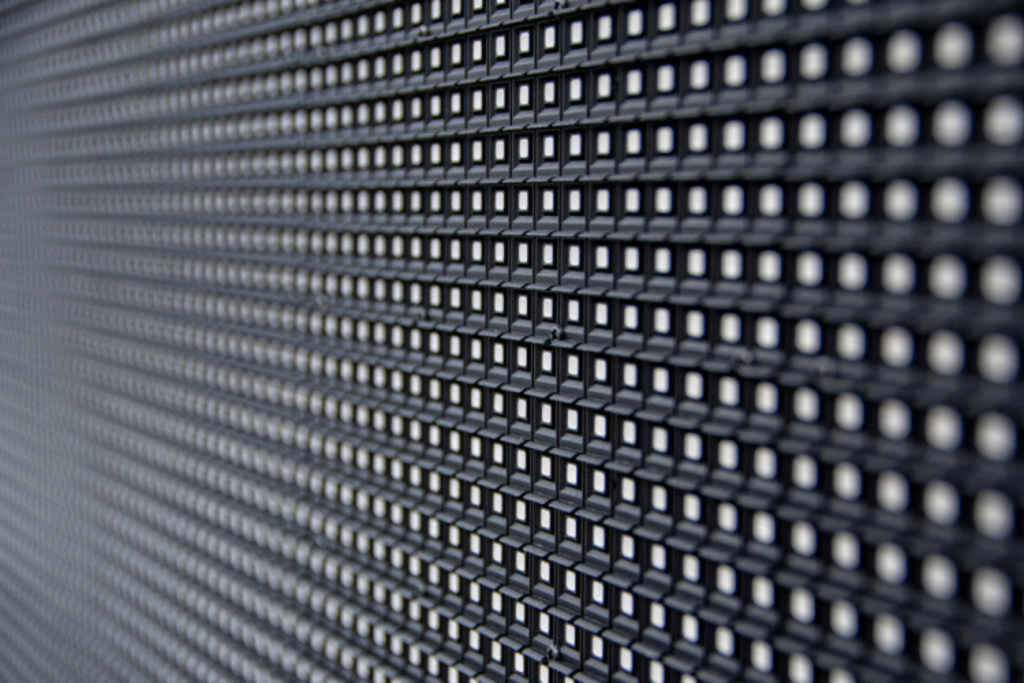
“Traditionally LED used gold thread technology because people were worried about the longevity of LEDs, so to be on the safe side they always use gold thread instead of copper thread LED.” What he has seen in the last five years is an increasing use of copper thread LEDs, driven by costs (copper is cheaper than gold thread LED). The difference in price can be up to 30%, so you can see why people would be tempted, but be aware that cheaper price comes at a cost says Burgess. “A lot of uneducated customers don’t know there’s a difference, or don’t ask about the difference. They’ll get a quote and one price is much lower than the other and they buy on that basis. If they investigated, they’d probably find that that cheaper LED quote is because it’s using copper instead of gold, and you won’t get as much brightness and it will consume more electricity because it’s slightly less efficient than gold. So whilst the capital cost is cheaper, your running costs and the efficiency the LED won’t be as good. I’m not saying there’s no place for copper thread LEDs, I’m just saying that it’s one of those things that any customer is buying should be asking, am I getting copper thread LED? Or am I getting gold thread LED?”
All ROE Visual’s LED products use gold thread says Prak, because it “chooses the highest quality parts and materials available in production to ensure a durable and stable performance of all our display types.”
That leaves us with the two newest LED technologies, called GOB and COB. Again, Burgess can provide some context. “The reason for the move to those two technologies is because LEDs when you get to a very tight pixel pitch (such as SMD) it becomes very fragile, and it’s easy to catch the edge of a PCB and knock off a couple of LEDs. Often the cost of doing that is not that you have to pay an engineer to resolder the LEDs, it may well be that in knocking off the LEDs, you’ve damaged the track on the PCB, and it’s damaged beyond economical repair, so it becomes quite expensive to do.”
COB (chip on board) technology again dates back to the early 2000s, when manufacturers began to realise instead of being soldered to the PCB you could bond it to the PCB, so it bypassed the wave soldering process. With SMD you can have up to 3 diodes within a single chip, in COB you can have 9 or more diodes. Regardless of how many diodes are soldered on an LED substrate, a single COB LED chip has only two contacts and a circuit. This has greatly reduced the failure rate. One of the biggest advantages of COB is that it can produce higher brightness with lower power consumption per square inch when compared to DIP and SMD. One disadvantage COB has compared to SMD is that more expensive to produce than SMD, and has lower colour uniformity.
The two most important elements in an LED production line are the pick and place machine which puts the LEDs in place and the wave solder machine that passes the PCB through with the LEDs in place (but not attached). It is then heated to 272 degrees centigrade, and that melts the LED and flows the solder into the right position. “But if you’re at 280 degrees or 260 degrees, and you don’t solder it properly, you might get damaged solder joints, and so consequently, the screen will be unreliable for its entire life. By going to COB you’re not relying on soldering, so that element doesn’t matter. COB is also more resilient, with an SMD screen you handle it very carefully, with a COB screen you can hit it with your shoe, and it still won’t break,” says Burgess.
A GOB display uses almost the same production technology as SMD, it just adds a transparent glue to provide a shield which makes GOB waterproof, dust-proof and less prone to damage. For buyers reading this wanting any advice, are there any of those four LED types that are particularly suited to indoor or outdoor installs or better suited for particular applications ie retail or controls rooms than others? The answer is yes says Roe Visual’s Marina Prak. “For the Virtual Production market, users usually strive for the best in-camera performance, so they would choose individual SMD LED products for better anti-reflection, contrast ratio, and higher uniformity, which are more important standards in the shooting process. LED products using UVA technology are another example. The technology applies to special-designed modules when used as LED ceilings, which helps LEDs get much better colour performance, reduce the colour deviation (colour shift), and improve uniformity. For retail applications, the COB LED product may be a better choice than SMD one for its better protection feature.”
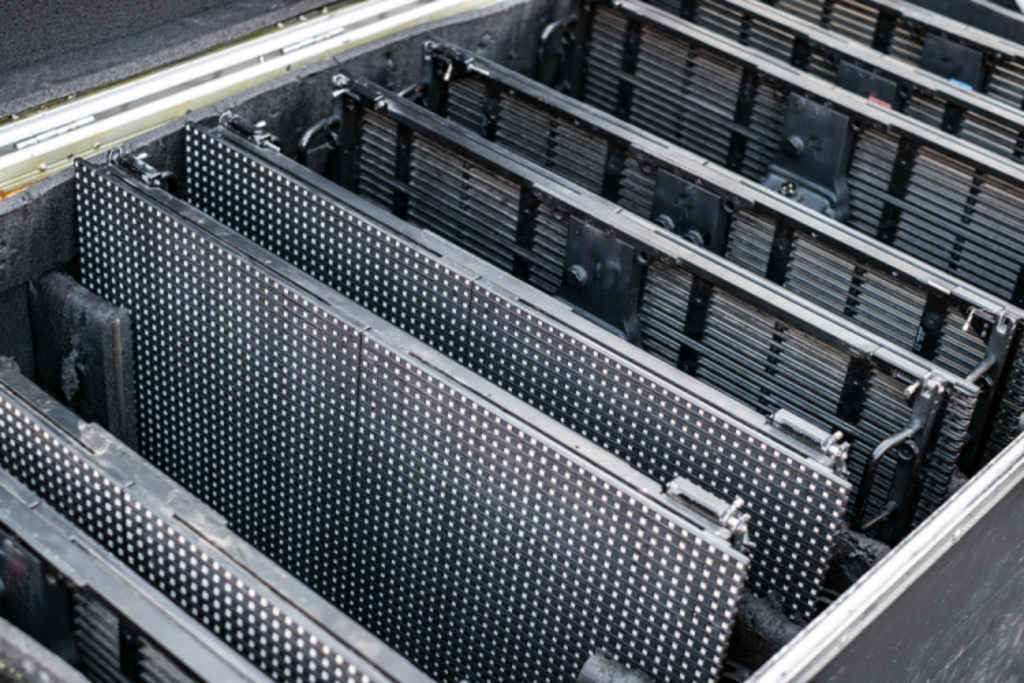
The advice from Burgess follows a similar path, “We only ever sell DIP now for 16mm or lower resolution. And that’s great because in an outdoor screen with long viewing distances, it’s really good on waterproofing, it’s very resilient, and it’s very bright, so it’s perfect for it. I’d say SMD is versatile, it can be used for lots of different scenarios. With COB you wouldn’t ever use outdoor because you just can’t get the brightness because of what you have to do with calibration, so COB outdoors is a no no.”
What questions should buyers be asking of their LED supplier? “What brand of LEDs are you getting? What type of LED technology are you getting? Gold thread or copper? I’d be asking what driver ICs (an integrated circuit that provides brightness and backlighting colour control) they’re using as well,” says Burgess.
“For brightness have a look at the spec sheet, but note that the brightness figures will be different before and after calibration, and thereby buyers should pay attention to this. For uniformity you need to focus on the uniformity data, usually expressed in percentage. For instance, if the data is 98%, then the largest brightness difference among all lamp beads on the panel is 2%. For reliability there are some key components to consider when measuring the reliability of a particular LED brand. The most obvious one is the raw materials used for the product, including chips, thread, etc. Then the understanding of the factory’s production process also matters, such as the details within each production step and quality control management. In addition, factory certification should be considered as well,” says Prak.
It’s clear not all LED screens are created equal, a short walk around any trade show will show you that. But its also important to know what’s inside your LED tiles, as components and manufacturing processes play a major part on quality, uniformity, purchase price and running costs. With so much choice in the market when it comes to LED, it’s definitely a case of being forewarned is to be forearmed.
top image: Olexandr Taranukhin/Shutterstock.com
middle image: Miguel Couto/Shutterstock.com
bottom image: Roberto Sorin/Shutterstock.com